Key Considerations in CNC Machining for Large Mold Manufacturing
On
22/12/2023Summary:
CNC (Computer Numerical Control) machining has become an indispensable technology in the manufacturing industry, especially in the field of large mold processing. This technology significantly enhances production efficiency and product quality through precise and efficient machining processes. However, CNC machining for large molds involves numerous complex steps. Thus, special attention must be given to several aspects, including material selection, machine configuration, machining processes, inspection, and quality control.
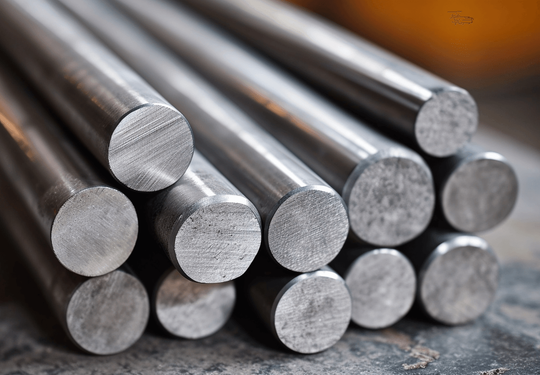
Material Selection
A. Types and Properties of Mold Steels
Common mold steels include P20, H13, and S7. P20 steel is widely used due to its moderate price, good hardness, and toughness, whereas H13 steel is often used for hot work molds owing to its high strength and high-temperature resistance.
Large molds typically require materials with superior wear resistance, hardness, and strength to ensure they can withstand prolonged high-stress operations.
B. Heat Treatment
Heat treatment is a crucial process to enhance the material properties. Common heat treatment methods include quenching, tempering, and annealing. These processes adjust the hardness and toughness of the mold steels, improving their service life.
Machine Configuration
A. CNC Machine Selection
For large mold machining, selecting the appropriate machine is essential. For instance, five-axis machining centers can handle complex geometries and are suitable for high-precision large mold machining.
The rigidity, stability, and precision of the machine are crucial factors affecting the machining quality. Large molds generally require high-rigidity machines to minimize deformation.
B. Tooling and Tooling Systems
Choose appropriate tools based on the material and machining requirements, such as high-speed steel tools, carbide tools, or ceramic tools.
The wear resistance and sharpness of the tools directly impact machining efficiency and surface quality, so regular replacement and maintenance are necessary.
C. Cooling Systems
In the machining of large molds, significant heat is generated due to friction between the tool and the workpiece. Cooling systems (e.g., liquid cooling, air cooling) play a vital role in preventing workpiece deformation and tool wear.
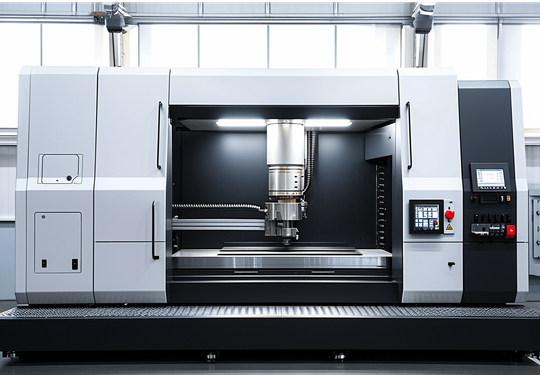
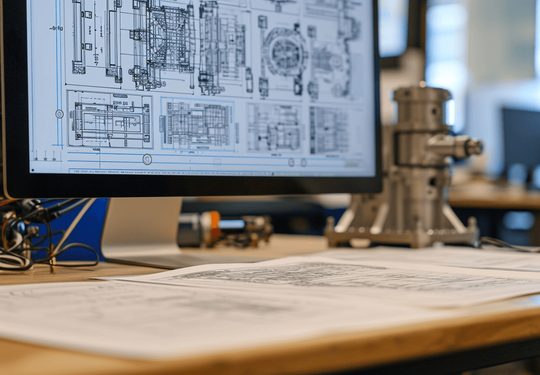
Machining Processes
A. Roughing and Finishing
In large mold machining, a step-by-step approach is typically employed, starting with roughing to remove the majority of material, followed by finishing to achieve the final dimensions and surface precision.
Roughing focuses on efficiency, while finishing emphasizes precision and surface quality, necessitating different tools and parameters.
B. Programming Techniques
CNC programming is critical throughout the machining process. It requires a strategic allocation of cutting paths, speeds, and feed rates based on the mold’s complexity and precision requirements.
Modern CNC machines are often equipped with CAD/CAM software allowing programmers to simulate the machining process, optimize cutting parameters, and reduce trial-and-error costs.
Inspection and Quality Control
A. In-Process Inspection
During machining, in-process measurement systems can monitor the dimensions and surface quality in real-time, enabling timely adjustments to ensure machining precision.
B. Final Inspection
Upon completion, a comprehensive inspection of the mold’s dimensions and surface quality is necessary. Common equipment includes Coordinate Measuring Machines (CMM) and laser scanners.
Focus on critical dimensions and areas to ensure all parameters meet design specifications.
C. Mold Testing and Adjustment
After machining, the mold should undergo testing to verify its performance in actual production conditions. Necessary adjustments and optimizations should be made to ensure optimal performance.
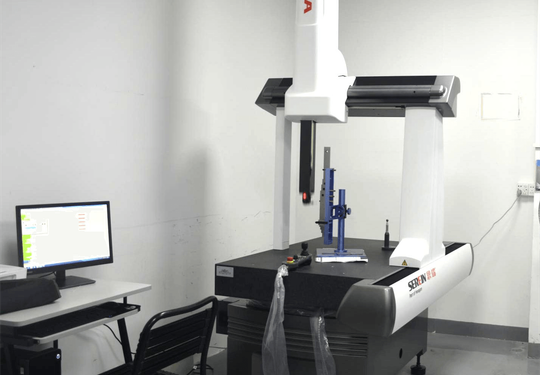
Conclusion
CNC machining of large molds is a multi-step, intricate process that requires high levels of technical expertise and management. By carefully selecting materials, configuring precise machinery, optimizing machining processes, and implementing rigorous quality control, manufacturers can ensure that their molds exhibit high precision, strength, and longevity, meeting the demands of various complex working conditions. These key considerations not only help improve machining efficiency but also stabilize product quality, attracting more customers. We hope this article provides valuable insights for your CNC machining endeavors in large mold manufacturing.