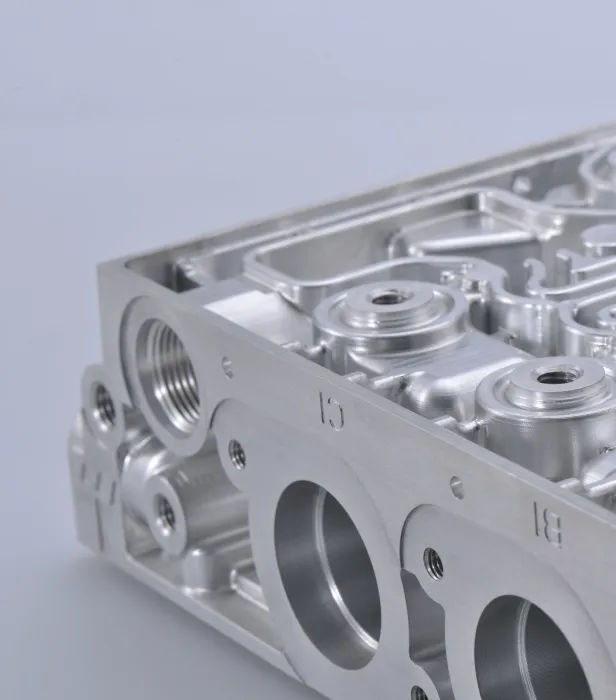
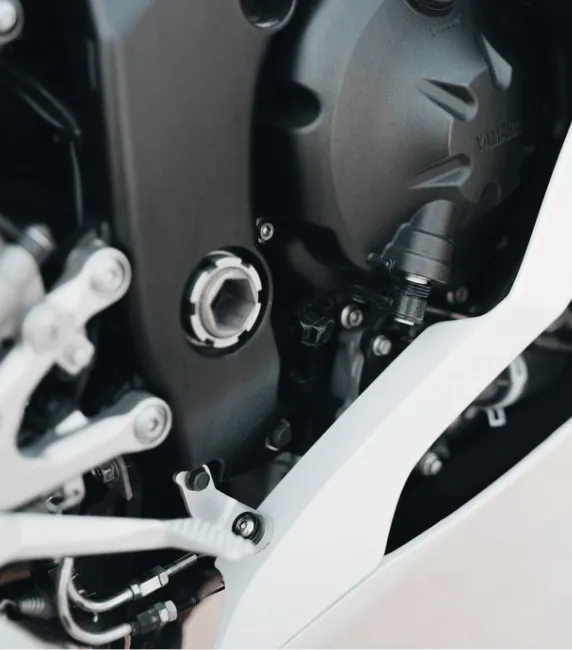
Molding
Well Proto delivers precision injection molding with advanced materials, ensuring durable, high-performance parts with a seamless journey from concept to market-ready products.
--Certificate : ●ISO9001:2015 ●IATF16949:2016
--All uploads are secure and confidential.
What is Molding?
Molding is a manufacturing process that involves shaping a pliable raw material by using a rigid frame called a mold or matrix.
This process is widely used for the mass production of parts and can be performed with various materials, including plastics, metals, glass, and ceramics. The raw material is placed into the mold, which is then closed and heated, causing the material to conform to the shape of the mold.
After cooling and solidification, the part is removed from the mold, resulting in a product that has the desired shape and texture.
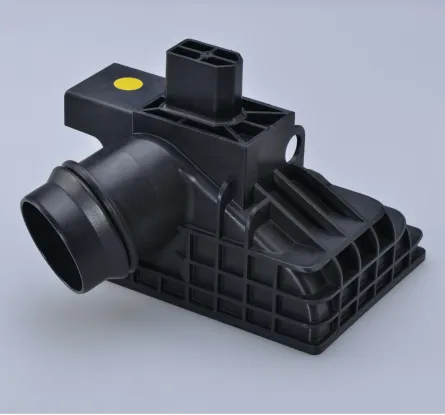
_9c9e0.png)
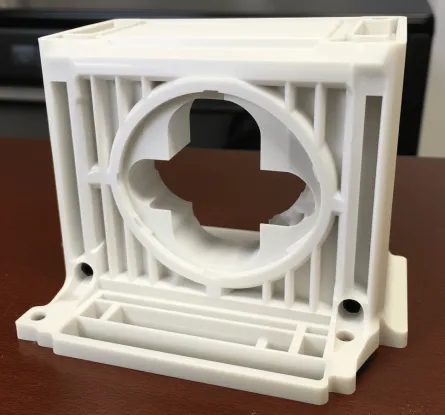
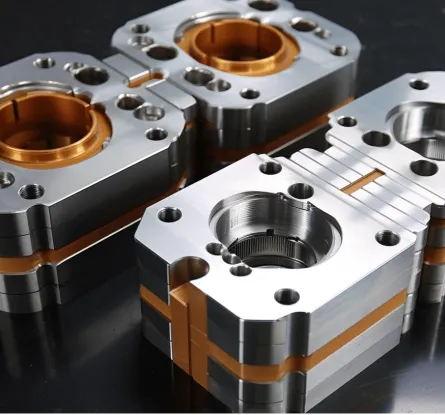
Well Proto's Molding Process
Our process begins with a consultation to understand the project requirements. Design for manufacturability (DFM) analysis is conducted to ensure optimal mold design and material selection. State-of-the-art CAD software is utilized to refine designs before they go into production.
Once designs are finalized, the chosen material is fed into our machines and the molding process begins. Throughout production, we conduct quality control checks to ensure every part meets our stringent standards.
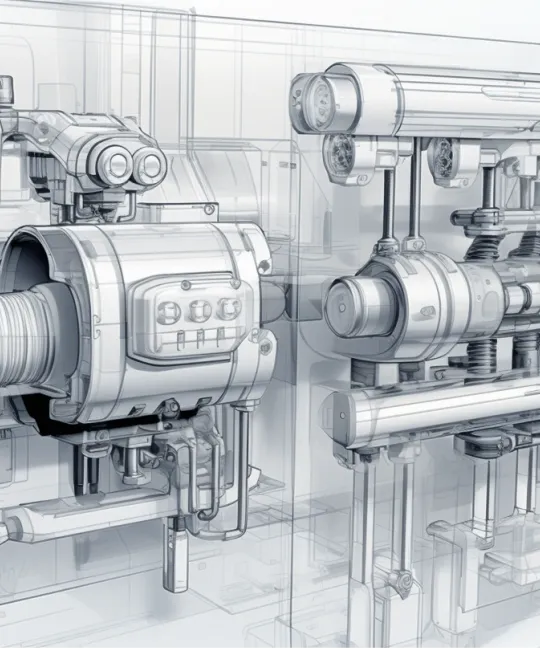
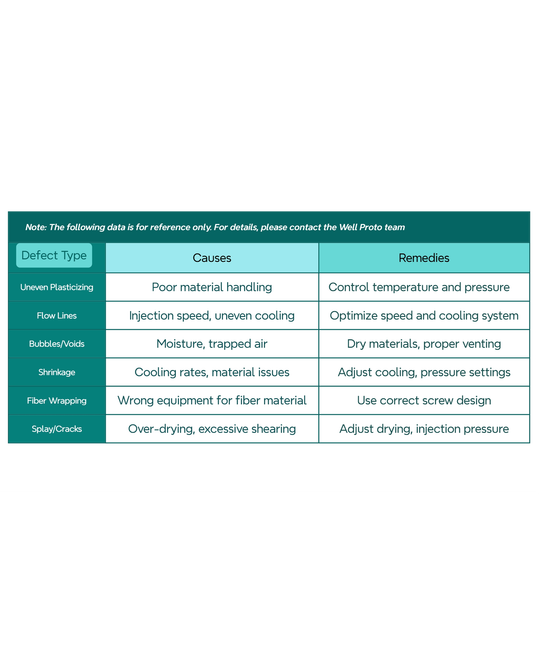
Excellence in Molding with Well Proto
Well Proto resolves common molding issues such as unstable plastification, flow lines, bubbles, voids, and sink marks, ensuring premium product appearance and integrity. Precise material processing, advanced mold design, and rigorous quality checks form the backbone of our approach.
Our use of scientific molding and 3D scanning guarantees consistency and flawlessness. By preempting defects and ensuring meticulous execution, Well Proto delivers top-tier molded products with superior aesthetic and structural quality.
Mold Maintenance Best Practices at Well Proto
Cleaning: Molds are cleaned immediately after use.
Lubrication: Moving parts are regularly lubricated to maintain smooth operation.
Temperature Control: Cooling systems are utilized to manage mold temperature during operation.
Storage: Molds are stored in controlled conditions to prevent damage.
Inspection and Repair: Regular inspections are conducted, and any minor issues are promptly repaired to ensure mold longevity and minimize downtime.
We aim to deliver precision-manufactured products through meticulous mold care and proactive maintenance, maximizing the lifespan of our molds and minimizing operational disruptions.
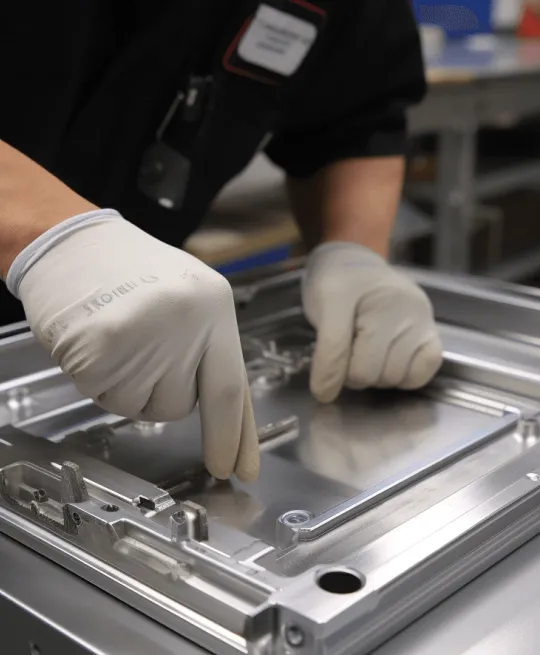
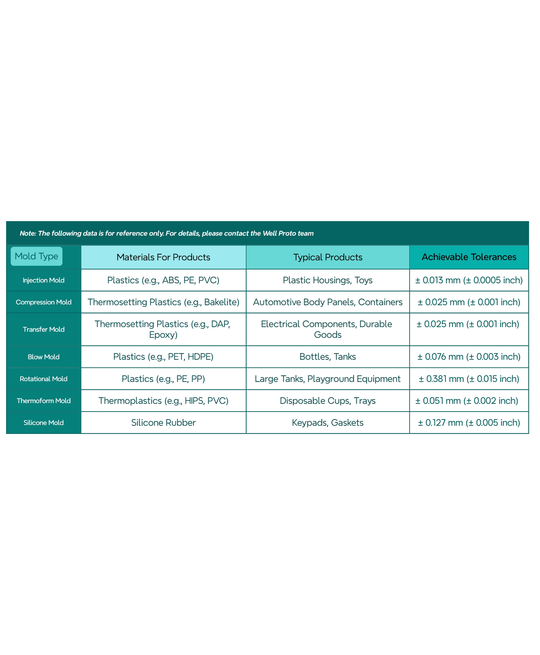
Customer-Centric Approach
We don't just provide mold machines, we provide tailor-made complete solutions. Our injection molding, blow molding and rotational molding services are all designed with our customers in mind, ensuring consistent and high-quality products.
Understanding the specific needs of each project and providing professional design optimization suggestions are the basis for our cooperation with customers. Contact us and let us help your project come to fruition quickly and successfully.
Key Aspects of Molding
High production efficiency
Molds enable mass production, greatly improving production efficiency.
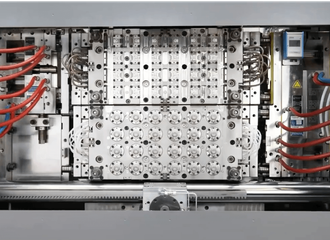
Cost-effectiveness
The unit production cost decreases as production volume increases.

Material versatility
Molds can be used with a wide range of materials, including plastics, metals, and composites.
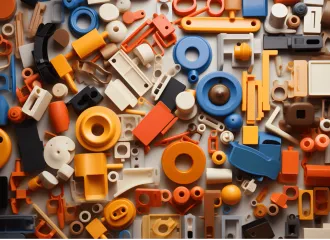
Don’t miss out on these amazing services below!