Tolerance Control in Precision Machining: Challenges and Solutions
By:
Well Proto Team
On
22/12/2023Summary:
In today’s high-end manufacturing, controlling part tolerances is critical. Even minute deviations can affect assembly precision and overall product performance. This article explores the common challenges in precision machining tolerance control, delves into key technologies, and offers practical solutions to help companies enhance product quality and competitiveness.
The Challenges: Common Issues in Tolerance Control
Precision machining faces several challenges in maintaining strict tolerances:
Machine Stability Issues:
Vibrations or instability in the machining process can lead to dimensional errors, affecting tolerance control.Tool Wear and Suboptimal Tool Paths:
Worn-out tools or poorly planned tool paths reduce machining accuracy, resulting in tolerance deviations.Temperature and Material Variability:
Fluctuations in temperature and inherent material stresses can cause thermal expansion or contraction, leading to dimensional discrepancies.
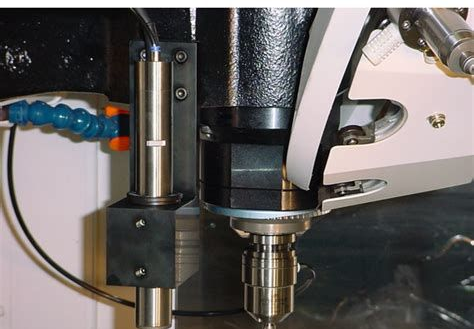
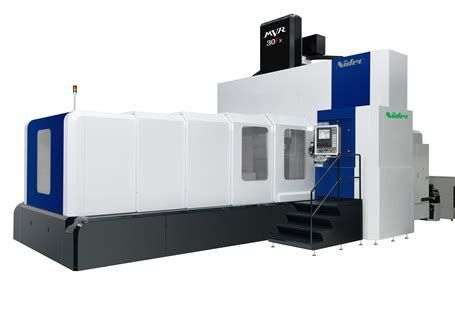
Technical Analysis: Achieving Precise Tolerance Control
To overcome these challenges, the industry employs several advanced techniques:
High-Rigidity Machine Tools and Intelligent Control Systems
Utilizing high-rigidity CNC machines combined with intelligent control systems minimizes vibrations and errors. Advanced shock absorption designs and automatic calibration ensure that every cutting operation is carried out under strict control.
Optimized Tool Selection and Path Planning
By using sophisticated CAM software, manufacturers can design optimized tool paths. Regular tool maintenance and timely replacement help reduce deviations due to wear. Simulation-based optimization not only boosts efficiency but also maintains tolerances at the micron level.
Environmental Control and Material Pre-Treatment
Maintaining controlled temperature and humidity in the workshop, along with pre-treating raw materials to remove internal stresses, helps reduce dimensional fluctuations from environmental changes.
Application Cases: Precision Tolerance in Key Industries
Aerospace Sector
In aerospace, components require extremely tight tolerances. Advanced CNC machining enables the production of critical parts that maintain dimensional accuracy even under extreme conditions, ensuring safety and performance.
Automotive Manufacturing
Automotive engine and transmission components demand high assembly precision. Precision machining with strict tolerance control significantly improves overall vehicle quality and safety.
Medical Device Production
High-precision medical devices require components to adhere strictly to design specifications. Precision machining technology ensures stability and accuracy, directly impacting patient safety and device performance.
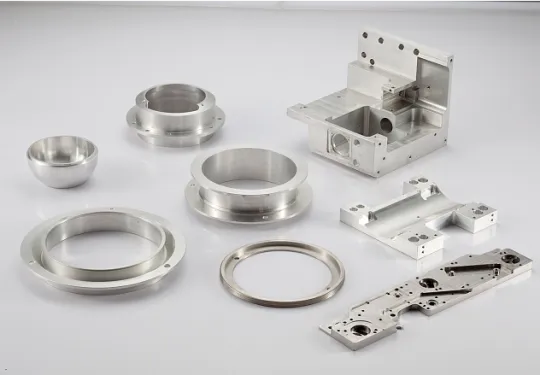
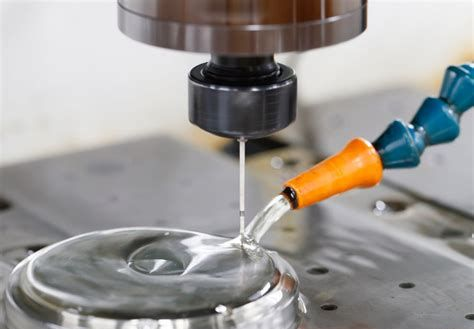
Future Trends and Outlook
As artificial intelligence, big data, and the Internet of Things converge, the future of precision machining will see further innovations:
Intelligent and Automated Upgrades:
Real-time data feedback and machine learning will make machining processes even more intelligent, further improving tolerance control.Virtual Simulation and Digital Twins:
Digital twin technology allows virtual testing and optimization of machining processes, enabling the early detection of potential errors.Green Manufacturing and Resource Efficiency:
The drive for sustainable manufacturing will lead to environmentally friendly processes that do not compromise precision while reducing energy consumption.